
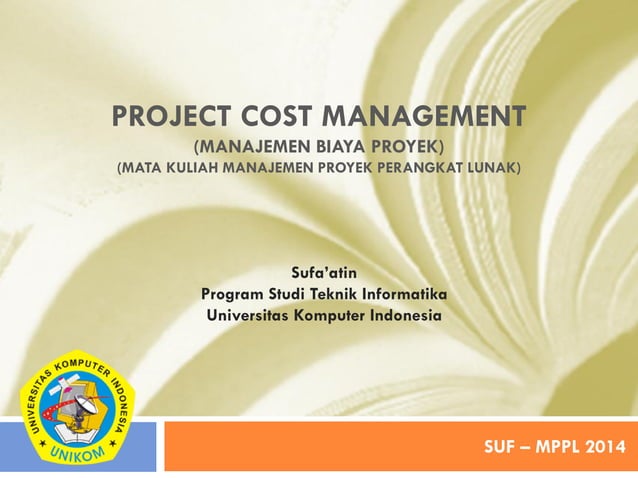
985,171,182.52 and after duration crash becomes Rp. 19.923.466,- due working time addition (overtime) to reduce project time with Time Cost Trade Off method. Crashing programme are do to 18 activities from 30 critical activies rescheduling with CPM result. Rescheduling with CPM result project completion time 120 days and after crashing project duration becomes 94 days, there was a reduction 26 days project completion time. Project A data is used to be a case studi in crash duration calculation and costs increase. This crashing planning is done by combining the Critical Path Method (CPM) and Time-Cost Trade-Off (TCTO) method for the minimum cost in crash duration calculation. Delay resolve method is to schedule crashing with various methods. Construction project delay can indirectly affect of project performance. Therefore the proposed model is proved has good accuracy.Construction delays are a common and major concern in most construction projects. The accuracy test of the model against the actual cost of the project showed 0.63% difference to the simulation results.
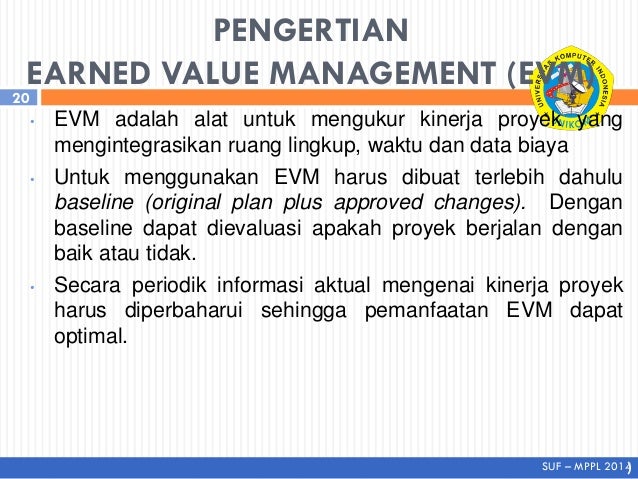
The results of case study simulation showed that the contingency cost is 4.57% of the project budget, with a deviation of 0.82%. For the purpose of model validation, procurement & Gas Piping Distribution project in Greater Jakarta was used as case study. Contingency cost calculation was done using Montecarlo simulations. Probability weights were analyzed using probability-Impact matrix and pair-wise comparison. Project Risks were obtained from preliminary surveys and literature studies. The objective of this research is to create a contingency-based cost estimation model by considering the types of risk and its impact on project activity. In fact, every activity has different risk and different weights of impact. Risks are assumed by providing lower and upper limit values of the cost of the risks that might occur in the project activity. This simulation techniques, despite widely used, still has the disadvantage.
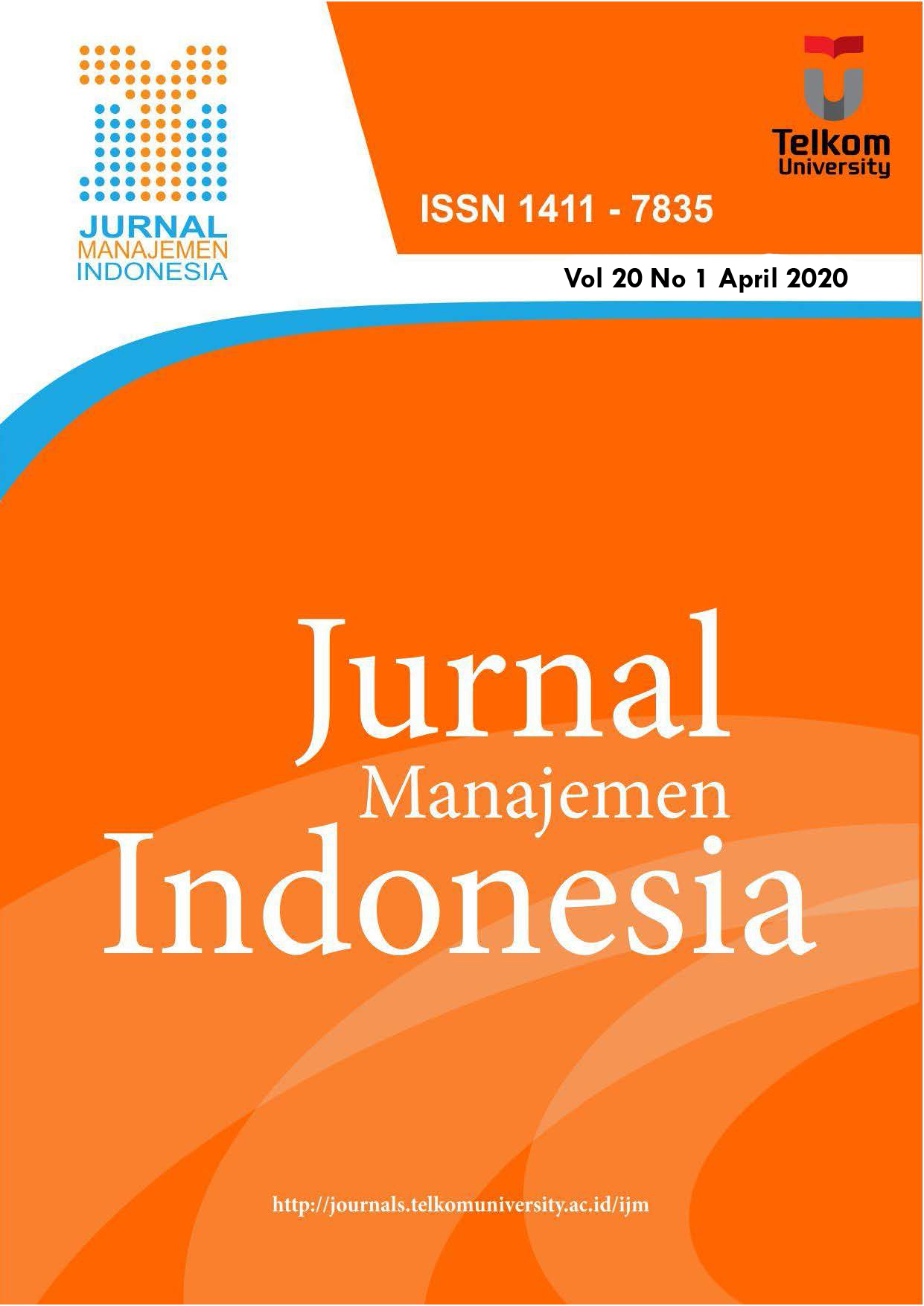
Currently, implementation of contingency estimation is done by directly increasing project costs by 5% -10% while in theory, the amount of the contingency cost is estimated using Montecarlo simulation techniques. To anticipate the risk of cost overruns due to the uncertainty, project implementers need to prepare the unexpected costs.
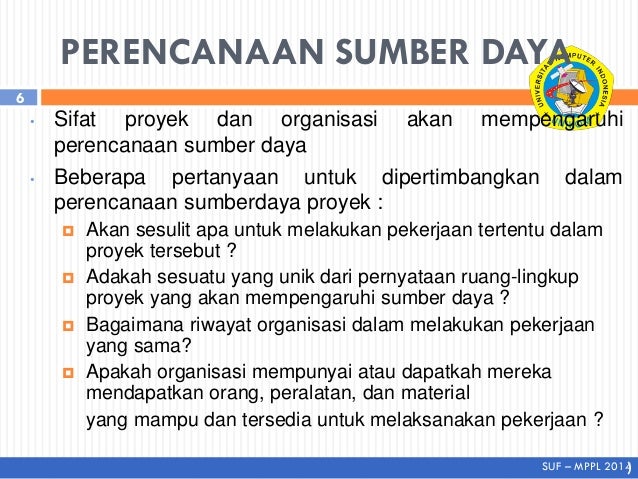
The complexity of EPC project resulted in many uncertainties that must be addressed by the project implementers. EPC (Engineering-Procurement-Construction) Project is a project in which the process of design, procurement and construction are carried out by a construction company.
